How To Repair Stucco Over Foam
Stucco Over Rigid Foam Insulation
Telescopic
Install stucco as an outside wall cladding over rigid foam insulation with proper preparation to provide water direction every bit well as a sound substrate for the stucco.
- Determine the location of the wall'southward water control layer (typically backside the insulation over the outside sheathing).
- Provide a drainage gap in front of the water command layer.
- Wink all windows, doors, and other penetrations to the h2o control layer prior to installing the insulation.
- Install stucco cladding per manufacturer requirements.
See the Compliance Tab for related codes and standards requirements.
Clarification
In response to more demanding energy codes, and equally occupants and domicile owners press for more than energy-efficient, thermally comfortable, and tranquillity houses, builders and designers are increasingly considering continuous rigid foam exterior insulation, even in warmer climates (zones 1-3), and with cladding types more common to those warmer climates. (Stucco is the bailiwick of this guide, but please note that adhered rock and tile follow the same principles).
With increased efficiency and comfort, however, besides comes an increase in the run a risk of water-related building failures (such every bit mold, rot, and odors) considering the outside insulation reduces the energy catamenia through the wall, which also reduces its capacity to dry. For this reason, it is essential that proper drainage is provided behind cladding materials such as stucco.
Installing stucco cladding over rigid cream insulation requires additional preparation to ensure proper h2o management as well as a sound substrate for the stucco. This involves determining the location of the wall'south water control layer (typically behind the insulation over the exterior sheathing), providing a drainage gap in front of the water control layer, and flashing all windows, doors, and other penetrations to the water control layer prior to installing the insulation. Later the insulation is installed, the stucco cladding may be installed per typical manufacturer requirements. Coordination betwixt the designer or architect and installing subcontractor is required.
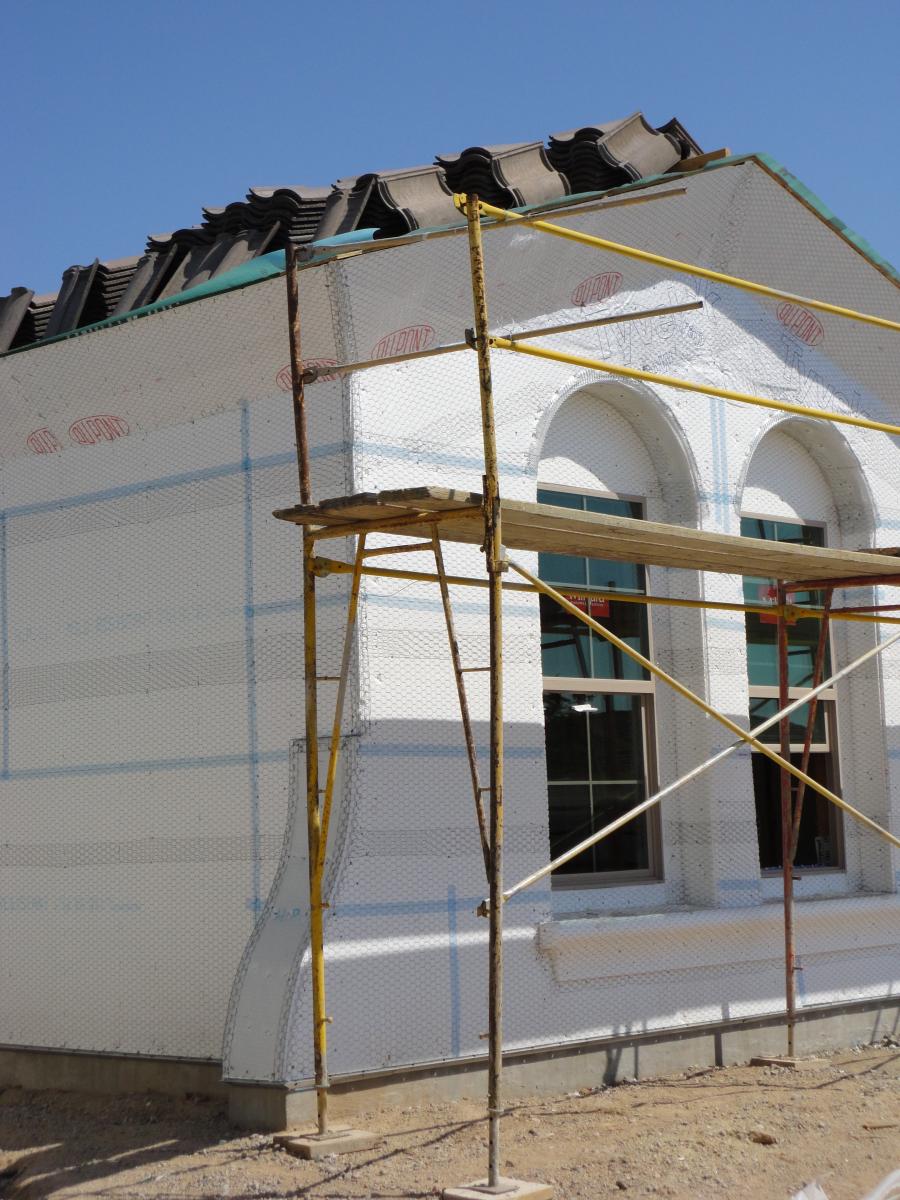
With respect to the location of the drainage plane, either over the face of the sheathing (behind the insulation) or at the face of the insulation, the old is far more common than the latter. Indeed, keeping the water control layer at the face of the outside sheathing means that standard window and door flashing details (and standard installation sequencing) are maintained – windows, doors, and other penetrations are flashed to the h2o control layer at the confront of the sheathing regardless of whether continuous insulation is used or not. When the confront of the insulation becomes the h2o control layer, window and door flashing details must be adjusted accordingly and a different installation sequence must be followed. That said, there are material (and perhaps also labor) cost savings associated with using the face up of the insulation every bit the water control layer (a separate membrane is no longer required).
The following guidance is for installations where 1.5 inches or less of continuous exterior rigid foam insulation is installed under the stucco cladding. Where more than than 1.v inches of continuous exterior rigid cream insulation is installed, additional structural support such as a 2d layer of structural sheathing (plywood or OSB) may demand to be installed over the rigid foam. In this case, the second layer of sheathing must be protected from disuse past installing a h2o control membrane over information technology with a drainage gap.
How to Install Stucco over Continuous Rigid Insulation
- Make up one's mind the location of the wall'due south water command layer (the drainage plane). Typically this volition be behind the insulation and over the outside capsule, only the face of the rigid insulation may besides serve as the wall's water control layer/drainage plane if the joints are taped.
- Install a water command layer (building wrap, self-adhered or fluid-practical membrane) over the face up of the exterior sheathing and flash all windows, doors, and penetrations to that layer. See Effigy 2. IRC 2022 requires the water control layer to be equivalent to ii layers of Grade D newspaper. Or, if the face of the rigid insulation is to exist the water command layer, tape the joints with acrylic sheathing tape or cocky-adhered membrane (which is recommended at the inside and outside corners for better adhesion) and flash the windows, doors, and penetrations to the face of the insulation.
- Provide a drainage space in front of the water control layer:
- If the water control layer (drainage airplane) is behind the insulation and over the exterior sheathing, the drainage space tin be achieved past installing a layer of textured firm wrap over a water control membrane. Alternately, cap nails tin be used equally spacers between the h2o control layer and the rigid insulation. The installer should utilise his or her professional judgment to decide the number of cap nails and the spacing required to provide a articulate drainage plane.
- If the water control layer (drainage plane) is the face up of the insulation, the drainage space can be achieved past installing a layer of textured edifice wrap over the insulation.
- For buildings that exceed two stories, are architecturally complex, or are built in locations that receive more than 20 inches of rain per year, the drainage space described above is insufficient, and a drainage mat (minimum ¼ inch thick) is recommended in lieu of the cap nail spacers or textured building wrap. Annotation that if drainage mat is used, it either needs to have an integral facer (typically a geotextile fabric) or a paper-backed lath should be used to prevent the pores of the drainage mat from becoming blocked with the subsequent application of the stucco.
- Install rigid insulation and tape the joints, even if the water control membrane is behind the insulation. This is non for water management but to maintain a continuous thickness of stucco. Maintaining continuity in the stucco across joints avoids differential rates of drying betwixt the thicker stucco at untaped joints and the thinner stucco over the field of the insulation. When the joints are left untapped, shadow lines tin appear at the joints from this differential drying. For the same reason, the material used to tape the joints should roughly match the absorption of the insulation. Acrylic sheathing record or cocky-adhered membrane is appropriate for XPS, while mesh tape is typically used with EPS insulations. After the above preparation, the installer may and so:
- Install lath and stucco in accordance with the manufacturer'due south instructions.
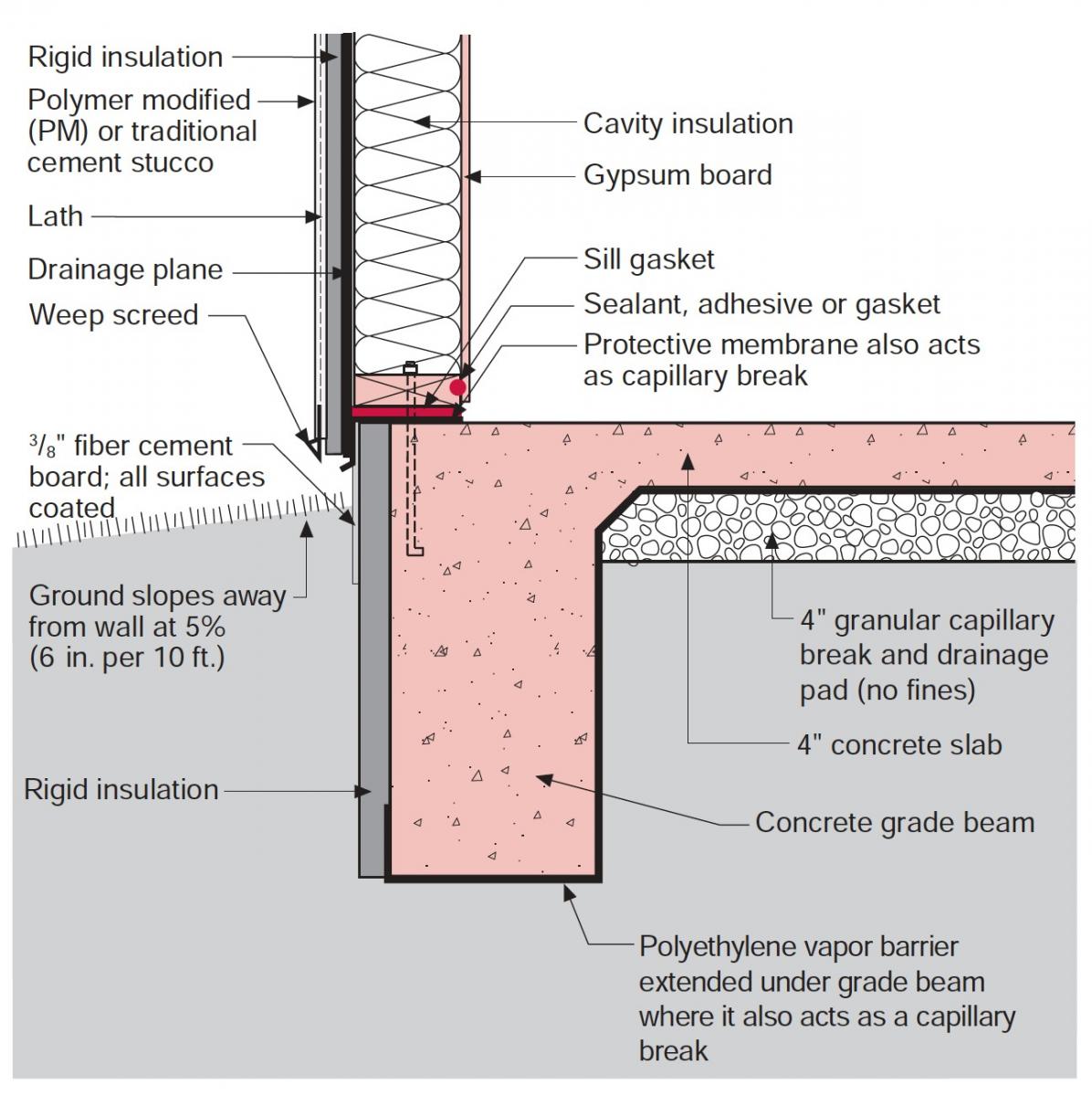
Ensuring Success
Ensure that all windows, doors, and penetrations are flashed and sealed to the water control membrane, not just to the face of the stucco. Install metallic or rigid plastic through-wall flashing at the base of the wall and strip it in with cocky-adhered membrane so that h2o running down the drainage plane is directed to the outside at the base of operations of the wall. Wherever possible, utilize flanged electrical boxes and flanged penetrations for better integration with the building'south water control layer.
Tape the joints of the insulation, even when the h2o control layer and drainage plane are located behind the insulation, to go along stucco out of the joints so that a uniform stucco thickness is maintained for even drying.
Climate
The location of the building will inform (1) the amount of drainage provided and (2) the amount of insulation in the assembly. If the climate receives more than 20 inches of rain annually, a drainage mat at least ¼ inch thick should exist installed over the water command layer.
For insulation thicknesses, consult the International Free energy Conservation Code (IECC) and the local building code. See the Compliance tab for more.
The Compliance tab contains both programme and code information. Code language is excerpted and summarized below. For exact lawmaking language, refer to the applicable lawmaking, which may crave purchase from the publisher. While nosotros continually update our database, links may have changed since posting. Please contact our webmaster if you find broken links.
The International Free energy Conservation Lawmaking (IECC) and ASHRAE Standard 90.ane are the codes and standards almost usually referenced past local jurisdictions and building certification programs (such every bit the U.S. Green Building Council'southward LEED) with respect to insulation in walls.
It is becoming increasingly difficult for opaque wall assemblies to comply with the prescriptive requirements of the IECC without the use of continuous exterior insulation, even when those walls are wood-framed residential walls.
The relevant prescriptive requirements for insulation in opaque walls can be establish in Table C402.1.3 of the IECC.
Insulation requirements for the 2022 IECC are shown in Table 1 beneath. Annotation that the first number in the recommendations for framed walls refers to cavity insulation and the 2nd (labeled ci) refers to continuous exterior insulation.
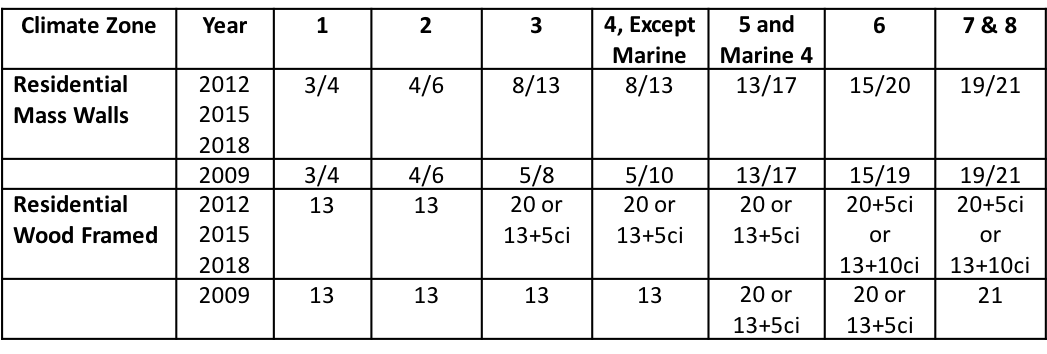
2018 and 2021 International Residential Code (IRC)
R703.vii Exterior Plaster (stucco)
Installation of plaster shall exist in compliance with ASTM C926, ASTM C 1063, and the provisions of this code. R703.7 and R 703.2: Water-resistive vapor-permeable barriers shall have a functioning equivalent to two layers of Grade D paper. The layers shall exist independently installed so each layer provides a separate continuous aeroplane. Install horizontally with upper layer lapped over lower layer by 2 or more inches, continuous to tops of walls. See IRC R 703.seven for specific requirements on board, plaster, water-resistive barriers.
Retrofit: 2009, 2022, 2022, 2022, and 2022 IRC
Department R102.7.one Additions, alterations, or repairs. Additions, alterations, renovations, or repairs shall adjust to the provisions of this lawmaking, without requiring the unaltered portions of the existing building to comply with the requirements of this code, unless otherwise stated. (See code for additional requirements and exceptions.)
Appendix J regulates the repair, renovation, alteration, and reconstruction of existing buildings and is intended to encourage their continued safe use.
Existing Homes
Telescopic
To retrofit an existing stucco wall:
- Remove existing stucco.
- Evaluate the sheathing and water control layer for harm.
- Appraise and repair causes of damage.
- Flash windows, doors, and other penetrations to new water control layer,
- Integrate new water control layer with existing walls assemblies.
Run across the U.Due south. Department of Energy Standard Work Specifications for more on adding exterior wall continuous insulation.
For more on working with walls, see the Pre-Retrofit Assessment of Walls, Windows, and Doors in the Building America Solution Center.
Clarification
To retrofit a wall system with stucco over rigid foam insulation, the existing stucco cladding must kickoff be removed. With the cladding off, the exterior sheathing and water command layer should be evaluated for impairment before to proceeding. Prior to replacing damaged sheathing and replacing or repairing the existing water command layer, it is of import to assess the crusade of any damage observed. Poor window flashing details and unsealed penetrations, for case, may need to be addressed independently of the new cladding work (by re-installing or replacing windows and penetrations and flashing them to the water control layer). Damage due to a lack of drainage in the original wall associates, however, can be addressed as part of the retrofit past providing a drainage membrane, mat, or spacers as described in the "Clarification" tab of the new home guide.
If the retrofit involves the installation of a new water control layer but the existing windows, doors, and other penetrations are to remain, they must be flashed to the new water control layer. To accomplish this, a portion of the existing h2o control membrane should exist left intact around these penetrations afterward demolition. The existing textile that remains should then exist shingle lapped and integrated with the new water control membrane with a uniform tape.
If only a portion of a building is to be retrofitted, ensure that the water control membrane of the new wall associates is properly integrated with the water command layer of the adjacent existing wall assembly. At vertical transitions a self-adhered tape or transition strip compatible with both membranes can be used. At horizontal joints (likely at a floor level) a metallic through-wall flashing is recommended (in lieu of simply shingle lapping and taping the water control layer to a higher place to the h2o control layer below). A through-wall flashing is especially important if the capacity of the lower wall assembly to drain water is poor or is unknown.
Follow the instructions in the Description tab of the new habitation guide for information on proceeding with the installation.
COMPLIANCE
See Compliance tab.
Access to some references may require purchase from the publisher. While we continually update our database, links may have changed since posting. Delight contact our webmaster if you discover broken links.
References and Resource*
*For non-dated media, such as websites, the appointment listed is the date accessed.
Contributors to this Guide
The following authors and organizations contributed to the content in this Guide.
Mobile Field Kit
The Edifice America Field Kit allows you to save items to your profile for review or employ on-site.
Sign Up or Log In
Did you find this data helpful?
Source: https://basc.pnnl.gov/resource-guides/stucco-over-rigid-foam-insulation
Posted by: loveshrich.blogspot.com
0 Response to "How To Repair Stucco Over Foam"
Post a Comment